10 Advantages of UV LED Technology for PCR-Grade Decontamination
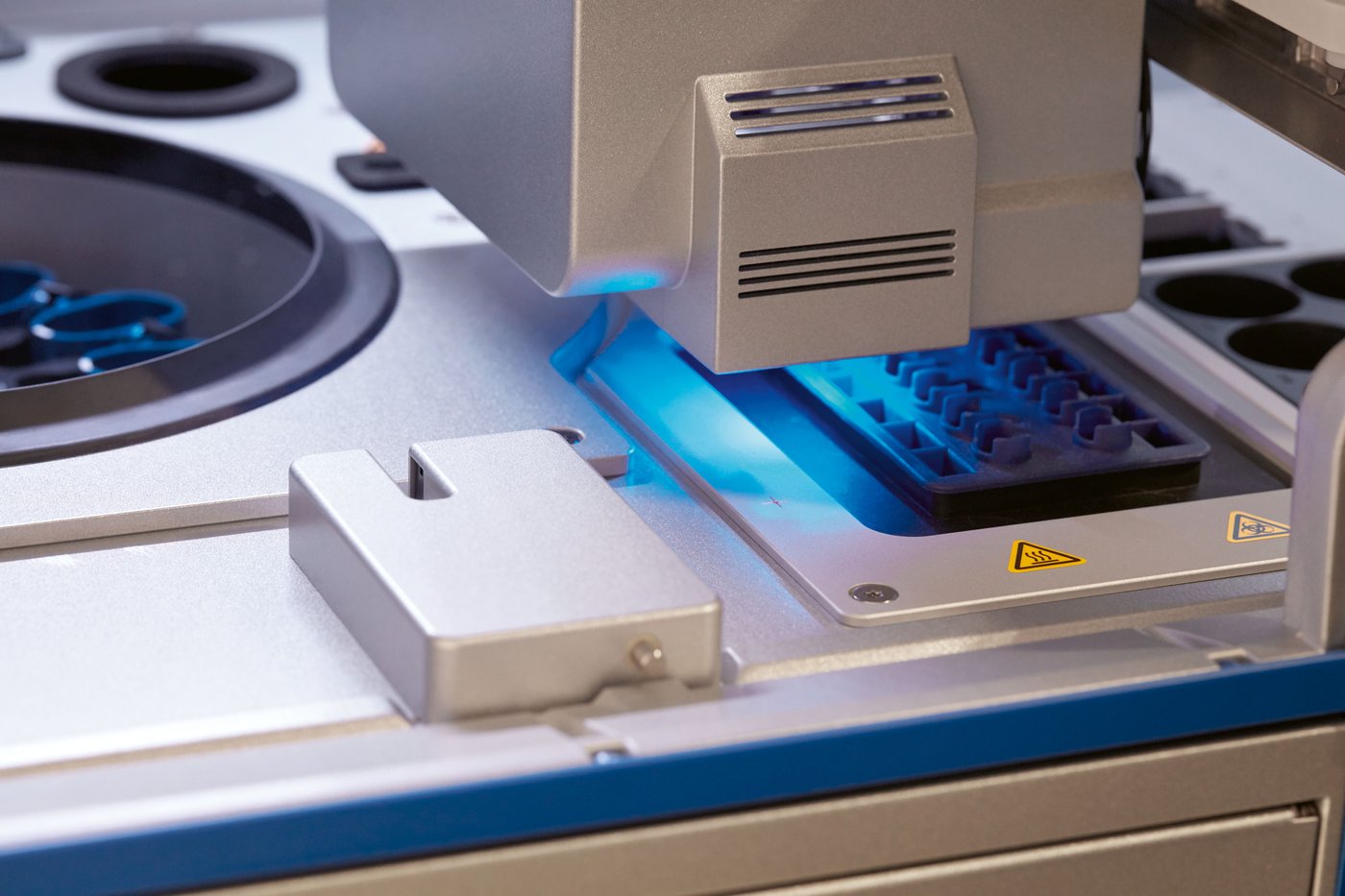
Posted by:
Harald Quintel
Published on:
Jan 9, 2020
Just like any other laboratory equipment, automated work decks need to be sterilized for successful experimental results.
ultraviolet (UV) irradiation, which stops bacterial, viral and protozoan replication in their tracks, and minimizes nucleic acid cross contamination.
The 200–280 nm wavelength of UV lights roughly overlaps with that of nucleic acids and proteins, which are vital for living organisms. Therefore, peak UV light emission at around 260 nm effectively damages nucleic acids as UV-C radiation causes chemical changes in DNA structure. The accumulating damage overpowers natural DNA repair mechanisms and eventually inactivates pathogens.
Effect of UV-C light irradiation on nucleic acids.
The most popular UV light emitters for instrument decontamination are low-pressure mercury vapor lamps, which have been the main UV sterilization method for the past 140 years. However, fitting mercury-filled tubes into modern automated systems is an increasingly restrictive factor for innovative device design.
For this reason, UV light emitting diode (UV LED) technologies have come to the fore as a powerful new method for decontamination based on 10 significant advantages:
1. Optimized decontamination
One of the greatest advantages of UV LEDs is their extended 280–260 nm emission spectrum. This spectrum as well as the 254 nm wavelength have different irradiation efficiencies that can be optimized to the desired pathogens. UV LEDs accurately decontaminate molecules within the wider 280–260 nm wavelength compared to conventional mercury power lamps.
UV emission spectra (nm) of LEDs VS low and medium power mercury vapor lamps (Source).
Furthermore, they can combine different UV wavelengths to maximize inactivation of specific bacteria (e.g., E. coli and B. pomilus) and viruses (e.g., MS2 and adenovirus 2) in work decks as well as liquids. However, more powerful UV LEDs are needed to irradiate highly resistant pathogens such as HIV.
To clarify, by decontamination we mean the reduction of pathogenic microorganisms to a level safe for human consumption. This includes reducing pathogens by at least 1 log level, i.e., 90%. Disinfection, in contrast, is a general term for reducing pathogen levels by a minimum of three and maximum of five logs.
To avoid cross contamination, UV technology should inactivate at least 99.99% of a given pathogen population. For bacteria and naked DNA/RNA, the minimal radiation dose required to reach these levels is 1,500–6,000 µJ/cm2.
Effect of UV irradiation on variety of pathogens (log scale).
2. Smaller lamp size
Most low-pressure UV lamps used range from 10–30 cm in size and contain multiple layers of glass and mirrors for thermal insulation and protection from the UV radiation and also a mounting system for the electric arc tubes inside.
In contrast, UV LEDs range from 5–10 mm in size, meaning they can be integrated much more flexibly into automated systems. They can be arranged in custom patterns and locations within an instrument, thus maximizing the decontamination area. Mini-sized LEDs thus enable new options for small reactor systems, point-of-use applications and integration into medical devices.
3. Environmentally friendly
Mercury power lamps are not an environmentally friendly decontamination method — low-pressure lamps need to be recycled to prevent the release of mercury into the environment, which requires specialized waste disposal.
UV LEDs are a great option for engineering greener instruments with lower environmental footprints. LED lights do not contain dangerous chemicals, which means they can be disposed of similarly to incandescent and halogen light bulbs or completely recycled. Additionally, electrical-to-UV C conversion efficiency of LEDs is already lower than that of mercury lamps and they consume substantially less power, making UV LEDs more energy efficient. UV LEDs can also be turned on and off instantly, whereas mercury tubes have a warm-up period before they reach full power, which means their energy consumption is less controllable.
4. Longer lifespan
In relation to the previous point, traditional low-power UV lamps have a short service life as they need to be replaced after around 1,000 hours of use and their output can deteriorate significantly as the bulb ages.
Conversely, UV LEDs last more than 10 times longer, with lifespans of over 10,000 hours. This means that UV LED decontamination can be run overnight to decontaminate more persistent pathogens.
5. Reduced overall cost
In the last decade, the price of UV LEDs has reduced from more than US$ 100,000 per mW to under US$ 1. You can find a UV LED lamp with 50 mW optical power for US$ 40, versus an equally powerful mercury lamp for US$ 700.
Due to no need for external power supplies and low starting voltages, the decontamination technology costs for an automated instrument can be reduced by up to 50%.
The development of UV LEDs in the last 5 years.
6. More suppliers available
Even though mercury vapor lamps are still the primary method for producing UV light, there are only a limited number of suppliers.
The rising popularity of UV LEDs has expanded their market more than five fold in the past decade, which is expected to reach over US$ 1300 million by 2025. Bigger manufacturers concentrate on LEDs with 10, 50, 100 mW power ratings, with 280 nm UV-B LEDs most commonly used in special applications e.g., ink curing and decontamination of liquids. Smaller manufacturers are more willing to offer small batches of high-power LEDs with power ratings higher than 100–150 mW.
7. Safer use
As mercury is considered to be toxic, mercury power lamps must be treated as hazardous. Mercury is a dangerous substance particularly in high-voltage and humid environments and implementing it into automated devices carries significant risks.
In contrast, UV LEDs don't contain mercury and nor do they require specialized handling or storage, which makes them a much safer UV source for both the instrument and the user. In terms of eye safety, there is no significant difference between mercury power lamps and LEDs.
8. No need for light redirecting
Mercury vapor lamps are omnidirectional, meaning they produce UV light in 360 degrees. At least half of the emitted light needs to be redirected to the target areas, requiring installation of a variety of reflecting mirrors inside an instrument.
UV LEDs, however, require minimal or no adjustment of optical elements as their light source can be easily directed to maximize emission.
Integrated UV LED module.
9. No regular cleaning required
Mercury lamps require periodical dusting and maintenance as their wide glass surface needs to be kept clean to allow maximum UV irradiation. The accumulating dirt burns into the top surface of the lamp, reducing the light reflected into reflectors and, thus, decreasing the irradiation efficiency.
In contrast, UV LEDs usually hang downwards, which prevents dust accumulating on top. However, the performance decrease due to dust accumulation in automated laboratory systems has not been measured.
10. Freedom to innovate
Based on all of the above advantages, UV LEDs elicit a new kind of freedom for automation system design. They do not require any special glass insulation, mounts or redirecting mirrors, so their installation is much simpler.
Multiple diodes can be arranged to emit light from different angles, in different sizes and to cover multiple specific wavelengths. Instruments no longer need to be designed around the UV decontamination lamps they contain, but the lamps can now be designed around the instrument. Advances in thermal management, optical configuration and hydrodynamic design are continuously improving the system performance and life span of UV LED decontamination systems.
These trends will create more options for effective and innovative engineering solutions in instruments for special applications, with high impact for future biological research and medicine.
Are you interested in using UV LEDs to decontaminate your automated systems? Read our checklist and discover everything you need to consider before implementation.