Reliability Engineering Builds Confidence by Making Failure Predictable
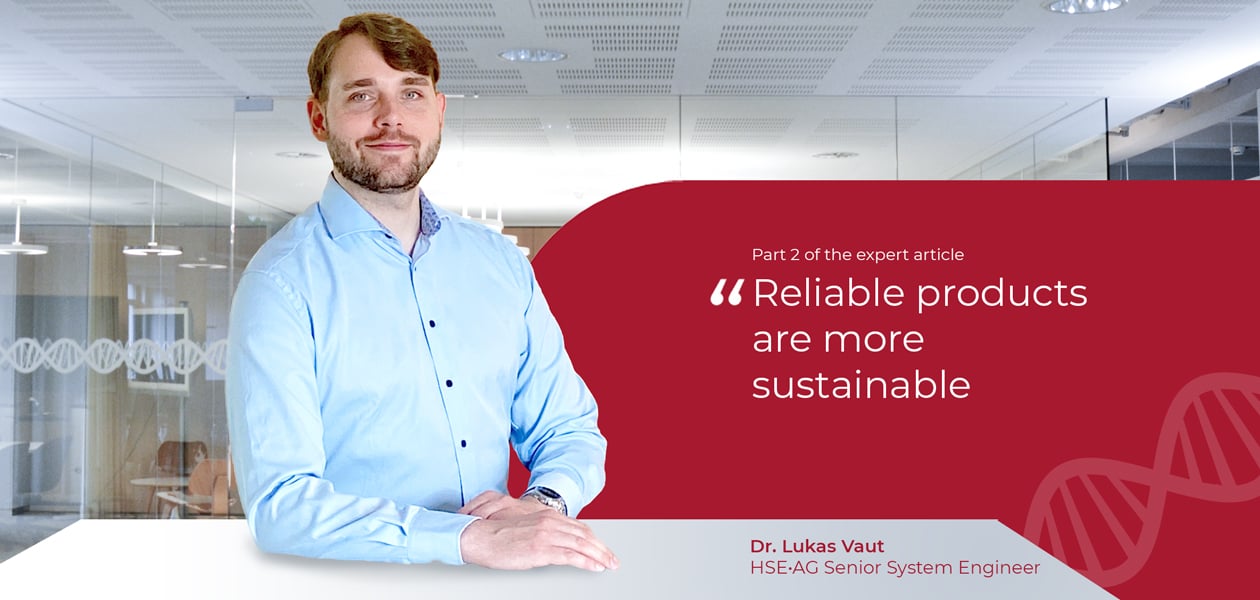
Posted by:
Lukas Vaut
Published on:
May 1, 2025
Understanding the differences between repairable and non-repairable systems is vital as this influences how we design, test, and maintain products. Discover in the second part of our two-part series how reliability tools are used to maximize system dependability and performance.
Repairable and non-repairable systems: Key differences
In reliability engineering, systems are classified as either non-repairable or repairable based on how they are managed after failure:
- Non-repairable systems: Once a failure occurs, the system is considered permanently failed and is either discarded or replaced.
- Repairable systems: After a failure, these systems can be repaired and restored to working condition.
Understanding the distinction between non-repairable and repairable systems is crucial for selecting the appropriate testing and analysis methods and maintenance strategies. Whereas a simple, low-cost mini-centrifuge may be considered non-repairable and discarded after failure, a more complex, higher-value centrifuge with extended functionality may be regarded as a repairable system.
Importantly, repairable systems can still include non-repairable components, like a centrifuge with a non-repairable rotor.
Therefore, thorough analysis of the system architecture is essential when assessing component versus system reliability.
Reliability Testing Goes Beyond Quality Control.
It is important to acknowledge that the reliability of a product cannot be assessed in a quality control setting. Quality control focuses on ensuring that a product meets specified standards at the time of inspection, either passing or failing based on immediate criteria – without considering the time dimension.
For example, a crack forming in the rotor of a centrifuge after 200 hours of use would not be detected. In contrast, reliability extends this concept over time, addressing the probability of a product performing successfully without failure over its entire lifecycle. Thus, reliability requires dedicated testing and analysis during the development stage, ensuring products are designed to perform successfully throughout their entire lifecycle.
Reliability introduces a time-based uncertainty, requiring probabilistic methods to forecast performance over prolonged periods. Therefore, it is essential that reliability requirements or specifications include both a time component and statistical confidence (e.g., R(1000h) = 90% with a confidence of 90%). Only then can they be clear, unambiguous, and verifiable.
Reliable products don’t just happen – they’re engineered and tested
Figure 1. Test to failure records when and how failures occur |
There are several approaches to reliability testing. Test to failure (Figure 1) is a method in which n samples of a component or system are subjected to continuous use until they fail, with the goal of recording when and how the failures occur. The data obtained can then be analyzed as discussed in part 1 of this article. |
If you only need to confirm a minimum reliability, a success run is a suitable approach for this (Figure 2).
Figure 2. A success run is suitable for determining |
In a success run, n samples are tested for the duration of the required minimum lifetime. If none of the samples fail, the reliability is confirmed with a certain level of confidence. The confidence level depends on the sample size, and increasing the sample size will increase the confidence of the result.
|
It’s important to note that in a success run, all samples must survive. If a failure occurs, it significantly impacts the required sample size to maintain the same confidence level.
Figure 3 illustrates how the required sample size increases depending on the number of failures in a success run.
Figure 3. Required sample size increases with number of failures
However, conducting a success run with multiple samples for the required minimum lifetime can be challenging due to the time and material resources needed. While sample size and test time are inversely related, it is possible to reduce both by applying certain acceleration factors or making assumptions about the underlying failure distribution.
Summary
This overview spotlights further aspects of reliability engineering:
- The difference between repariable and non-repairable systems
- Reliability testing
Using specific examples related to laboratory systems, the article guides you through practical approaches to understanding system behaviour over time and implementing test methods that support robust and reliable product development.
We support your success
As a global systems engineering provider with a proven track record in life science and diagnostics, we recognize your need for highly reliable products. We are committed to integrating reliability factors early in the product development process.
At HSE, we ensure the products we design not only meet but exceed market demands, focusing on dependability, resilience, and quality to support your success.
Contact Lukas Vaut and discover how our deep application knowledge and technical expertise can help you achieve the reliability you need.
👉 Don't miss the first part of Lukas' article, which guides you step by step through teh definition of reliability.
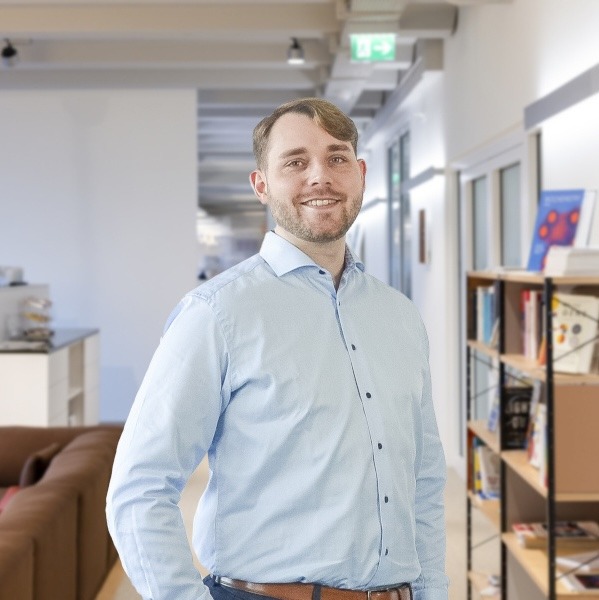
Reliability Engineering Expert Dr. Lukas Vaut
Lukas Vaut is a Senior Systems Engineer at HSE•AG bringing a wealth of experience in life sciences, pharmacy, and engineering to his role. With a BSc and MSc in Biosciences and a PhD in Health Technology from the DTU (Technical University of Denmark), his research focused on innovative 3D-printed microdevices for oral drug delivery.
Before joining HSE•AG in July 2023, Lukas deepened his knowledge of reliability engineering by taking up positions as a Development and Requirements Engineer at Resolve Biosciences and the Evident Technology Center Europe.
In addition to his technical expertise, he is a Green Belt® in Reliability Engineering and an IREB® Certified Professional in Requirements Engineering, ensuring robust and efficient system designs.