10 Keys to Successful Fluidics Projects
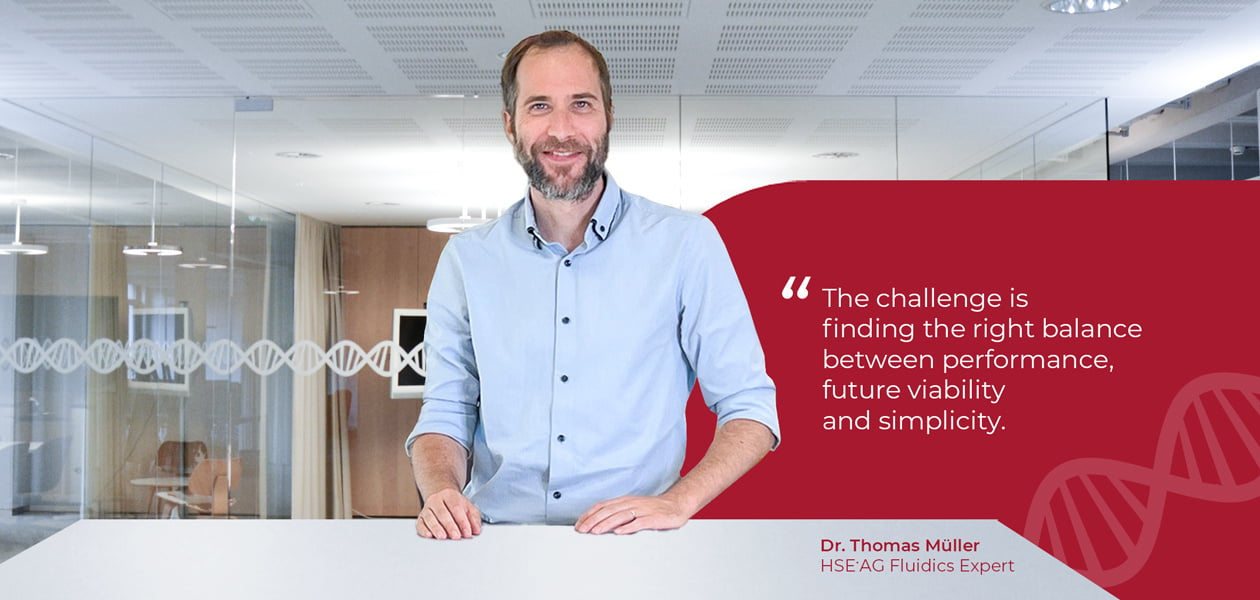
Posted by:
Thomas Müller
Published on:
Nov 5, 2024
For a fluidics development project, many areas must be combined under one system umbrella. The trick is to keep future options open while keeping things as simple as possible. It is worth investing time and a great deal of thought right from the start.
Set priorities in the initial phase
A total of 10 areas can be identified (see box “10 factors for successful fluidics devices at a glance”) that need to be addressed in a development project for a diagnostic device. Not all 10 areas are equally important in every project. Nevertheless, all areas must always be considered, at least in the initial phase, so that they can be ranked lower on the priority list with minimal risk.
10 factors for successful fluidics devices at a glance
Combining requirements under one system umbrella
The biggest challenge is not just fulfilling each individual requirement to the best level possible - that is a basic part of engineering. The difficulty lies in the fact that the overarching design goals almost always require a careful balancing act of tradeoffs. Thus, what truly is game-changing is the expertise of the development team in combining all goals and requirements under one system umbrella.
The frequently underestimated user experience
The area that is most often underestimated and consequently frequently overlooked, in my experience, is the user interface. This applies not only to the user interface of the device, but also to its integration into laboratory workflows. This neglect is even more surprising given that usability has a direct impact on market success. A device that is not compatible with practical workflows will simply be ignored by users.
To develop devices that meet the actual needs of users, a developer must not only be able to handle the device technologies and their interactions, but they must also be able to understand the realities of the laboratory. This includes incorporating specific factors, such as the height of the operating personnel or the use of laboratory gloves, into the design, along with the handling details of the upstream and downstream steps.
The area that is most often underestimated
and frequently overlooked is the user interface.
Performance and reliability: dependent on many factors
Accuracy, precision, and reliability are fundamental in diagnostics. They depend not only on precise liquid handling technologies and reliable components. The mutual compatibility of all materials, chemicals, and sample preparation methods is just as important.
For a risk-based assessment of compatibilities, the relevant tables in the technical literature are often inadequate. Instead, in-depth specialist know-how is required. At HSE, we have both extensive internal expertise, and a comprehensive partner network of specialists developed over many years that we can leverage for this purpose.
Consistent testing reduces risks
While however, in almost every project, new questions arise that cannot be adequately answered with the existing expert knowledge. In these cases, practical tests are necessary. This is especially true for components identified as critical in the risk analysis conducted at the beginning of the project. HSE has professional production and testing infrastructures. Many tests can, therefore, be conducted efficiently in-house.
Improve reliability? Change as little as possible
Improving the reliability of an existing system presents a particular challenge. The principle here is to change only as much as necessary, as every change carries a risk. This is especially true for the fundamental architecture of the device. A change affects many parameters, all of which must then be readjusted. The architecture should, therefore, only be changed if it is the actual cause of the problems.
Improve reliability?
Change as little as possible.
Economically critical: Serviceability
One aspect that is becoming increasingly important – and is closely related to reliability – is the serviceability of the device. Service contracts and innovative business models, where the device itself is no longer sold but, for example, the number of successfully completed measurements is billed, make efficient maintenance a critical factor for economic success. Components that show signs of wear must be quick and easy to replace.
As a basis for quality control, process optimization, and future use of machine learning, a sensor-based real-time monitoring system should be implemented that continuously reports the status of critical components. Since the exact sensor requirements are often difficult to assess at the beginning, it is beneficial to allow space for additional sensors.
Finding the right balance to enter the market quickly
One of the most challenging tasks is finding the right balance between performance, future viability, and simplicity. On the one hand, it is essential to keep options open for expanding into additional lucrative markets. On the other hand, unnecessary design contingencies pose risks, slow down the project, and extend the time-to-market, which is a critical success factor for many manufacturers.
To bring a new product to market as quickly as possible, many manufacturers opt to launch a simple first generation of the device. Only with the second generation does a version emerge that can be scaled for the future and adapted to additional target markets. Such strategies must be aligned early on with all stakeholders.
One of the most challenging tasks is finding the right balance
between performance, future viability, and simplicity.
Sustainability becomes a selling point
The sustainability of an analytical solution is becoming an increasingly important topic. The extensive testing during the COVID-19 pandemic clearly highlighted the substantial material consumption involved in in vitro diagnostics. More and more manufacturers are therefore identifying the efficient use of energy and consumables as a strong selling point. Clever design decisions can specifically minimize both the quantity of consumables and energy consumption.
The time invested at the start pays off
The numerous aspects that must be considered when developing fluidics-based analytical devices make it clear that it is worth investing time and energy at the start of the project to address fundamental questions. The more application knowledge and market understanding the development partner can contribute, the more successful the outcome.
Fundamental questions include the choice of optimal system architecture and the appropriate fluidics design principles. Depending on whether consistent flow rates, rapid dispensing of small volumes, or the even distribution over a larger area is critical for the application, a different fluid control system must be chosen.
The design process must also include all relevant regulations and certification requirements from the outset. Subsequent adaptations are time-consuming and costly. HSE has extensive project experience and a team of proven experts who, thanks to decades of experience, understand what different environments require.
Discussions on simplification must take place on an ongoing basis
The discussion of simplification cannot be completed in the initial phase. It must be conducted on an ongoing basis. At the start, for example, it is not only worthwhile allowing space for additional sensors, but also for additional valve controls.
However, it is impossible to continually keep space available for all eventualities. How much space is left in the design at a certain stage of development and what is removed must, therefore, be continuously renegotiated until the project is successfully completed.

If you're working on a project, our Fluidics Expert Dr. Thomas Müller, along with our HSE expert team, is ready to assist:
- Collaborative Solutions:
Whether you're in the early stages of development or looking to refine an existing system, our HSE expert team can provide insights and recommendations based on proven strategies. - Custom Fluidics Design:
If you need tailored solutions, our HSE expert team can advise how to adapt fluidics components. - Problem-Solving & Troubleshooting:
Facing a challenge? Our HSE expert team's extensive experience across various projects enables them to resolve
performance issues or inefficiencies in your fluidics systems.
Feel free to reach out to discuss potential collaborations or ask any question about fluidics engineering:
Just call: +41 55 254 04 00, send an email or view Thomas' profile on LinkedIn.
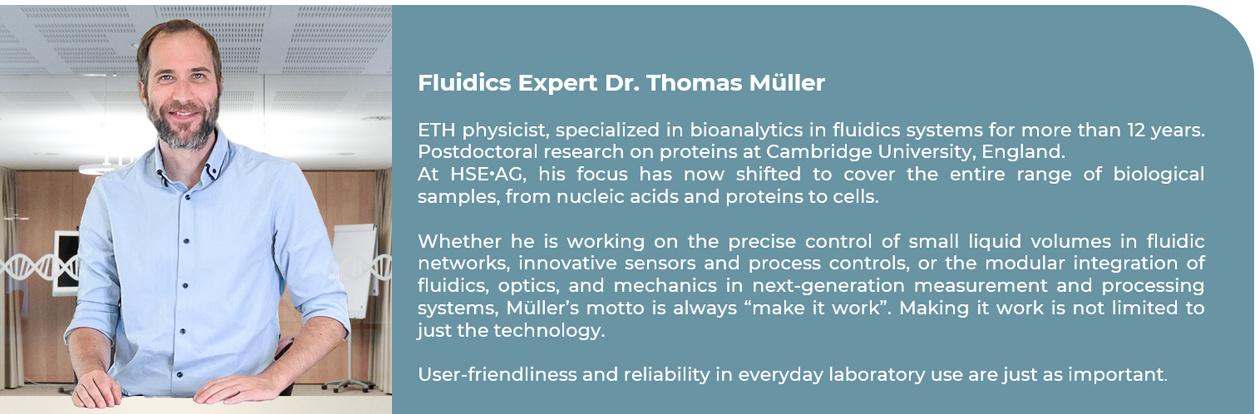