The Engineering Key to Economic Syndromic Testing Success
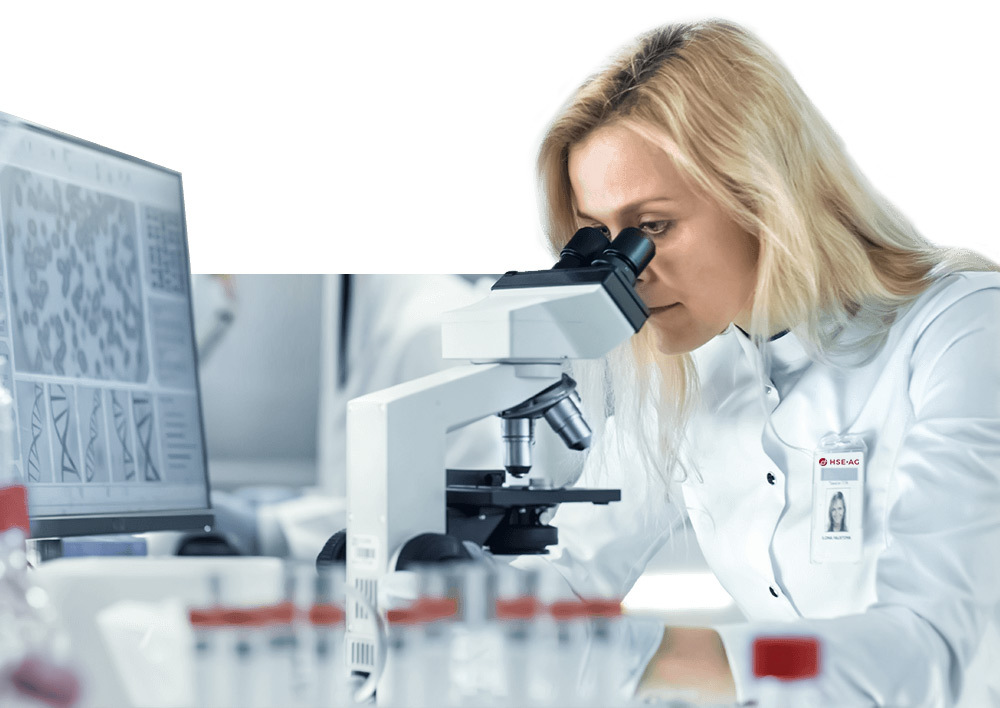
Posted by:
Hans-Jürgen Tiedtke
Published on:
Nov 23, 2021
Syndromic testing is one of the big growth promises of the coming years. However, it takes more than just exceptional scientific innovation for an assay to become a market success. To be commercially successful, the method also needs to be intelligently automated. For this, engineers need to know and understand both the cost drivers and the laboratory processes in detail.
Roche’s acquisition of GenMark in the spring has turned the spotlight on a young diagnostics market with enormous growth potential: syndromic testing. This uses multiplex PCR methods to simultaneously test for the presence of as many pathogens as possible that may be responsible for a specific clinical picture. Compared to conventional diagnostic procedures, usually based on cell culture, this saves a huge amount of time and plays a key role in starting effective treatment as quickly as possible.
Many fail when it comes to economic viability
From an engineering perspective, simultaneously running and evaluating many PCR assays presents a number of demanding challenges. This is because the system must not only meet the biological requirements of the test procedure and perform the physical handling and measurements accurately and reliably. The bottom line of the tests must also make economic sense. Experience has shown that many providers fail precisely when it comes to this last requirement. They fail to transform their biochemical innovations into a marketable product.
Point of need additionally increases demands
This is especially true if the method – as with syndromic testing – should not only work in specialized laboratories, but also as a point-of-need application that can be performed directly in hospitals by medical-technical assistants without special training. The entire test, including as many of the reagents as possible, must be provided in a single cartridge. This must be suitable for storage, and the human handling required to perform the test must be simple and kept to a minimum.
Cartridge complexity drives the price up
Prefilled reaction vessels require strict separation of dry and wet areas. While the biochemical processes take place in a closed plastic cartridge, physical handling steps such as heating and cooling or control of liquid movement and detection from the outside are carried out via corresponding interfaces in the cartridge.
This means the cartridge has to meet extremely varied and complex requirements. It must be possible to heat this rapidly and cool it again in the PCR areas and, in other places, the plastic must be permeable to the detection method. In addition, the design should also allow for the most efficient liquid movement possible. It is important to reconcile all these demands as simply as possible because the cartridge, as a consumable, usually becomes one of the biggest cost factors for users. Any reduction in complexity greatly improves cost-effectiveness.
Engineers need to understand the laboratory applications
One of the most important causes of subsequent failure is an error in the process, often made before the actual development work begins: too little time and energy is spent on simplifying the biological process as much as possible. However, it is not just the test manufacturers’ specialists with their biology and chemistry know-how who are needed. The engineers who develop the technical system are equally as crucial.
The better they understand the laboratory assay, the more specifically they can question the scientists. The more experience they have in a wide variety of automation projects, the deeper their knowledge of the key components that can lead to sources of error and price increases. Therefore, the engineering side always needs in-depth biological expertise in addition to the technical system know-how. This is the only way that a fruitful dialog can be created between scientists and engineers.
Small adjustments with a large price impact
For example, it often turns out that the accuracies for the temperature or volume specified by scientists in their requirements are not necessary for robust test performance. However, they impact the cost of many system components, from the materials and design complexity of the cartridge to the size of the heating elements and liquid-handling performance.
On the other hand, the number of beads used in magnetic handling, for example, can usually be increased without any major concerns. They have a minimal impact on the final price of the tests. The aspiration of a good instrument developer is not so much scientific excellence, but – in terms of the instrument and especially in terms of the consumables – to achieve optimal accuracy, reliability and cost.
Syndromic testing market trend
The characteristics of a disease and clinical findings often cannot be clearly assigned to a specific pathogen. This is especially true for respiratory or blood infections and for inflammation of the gastrointestinal tract or central nervous system. Until recently, elaborate cell-culture tests were necessary to filter out the pathogen responsible in each individual case from the many possible pathogens. So-called syndromic testing massively simplifies and accelerates analysis by using multiplex PCR methods to simultaneously test for many pathogens. Syndrome-specific panels can currently detect up to 30 viruses, bacteria, fungi or parasites each, as well as antibiotic resistance. The first panel for respiratory infections was approved by the Food and Drug Administration (FDA) 10 years ago. Meanwhile, several providers with different approaches and numerous syndrome-specific panels are already on the market. Therefore, it is increasingly more challenging to become successfully established in this rapidly growing analytics market.
Mr. Tiedtke has worked in the medical device and diagnostics industry for 25 years and is an expert in developing complex systems into finished, approved products. He has since acted as Head of R&D and Managing Director for multiple medical device companies.
Leading HSE•AG’s Engineering Technologies, Hans-Jürgen oversees the systems technologies and applications context of our customer’s projects. He combines the understanding of customer needs with analytic skills and creativity providing innovative solutions for complex life science tools and diagnostic platforms.